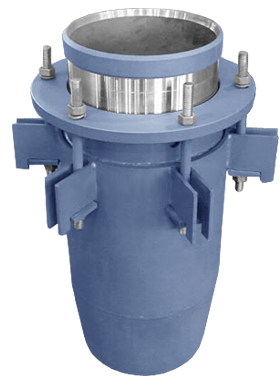
Основная трудность при изготовлении сальниковых и манжетных компенсаторов — это обработка патрубка, что объясняется большими отклонениями размеров труб, используемых в качестве заготовок. Рекомендуется подбирать заготовки путем измерения диаметра труб по всей длине, с учетом того, чтобы после проточки толщина оказалась не ниже минимально допустимой, указанной в чертеже. Если качество труб низкое и подбор заготовки невозможен, то ее вальцуют из листа.
Наиболее рациональный способ обработки наружной поверхности патрубка — бесцентровое точение. Его принцип заключается в совмещении двух движений: вращения резцовой головки и поступательного движения трубы через эту головку. Для этой цели применяют специальные бесцентрово-токарные станки (рис. 1).
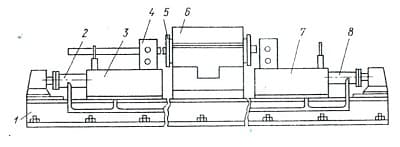
Рис.1. Бесцентрово-токарный станок
Станок состоит из станины 1, на которой жестко, закреплена шпиндельная бабка 6, а на салазках станины установлены загрузочная 3 и разгрузочная 7 каретки, перемещающиеся с помощью гидроцилиндров 2 и 8, Каждая каретка имеет гидравлические зажимы 4 для трубы, а шпиндельная бабка — специальные направляющие ролики 5.
Станок работает следующим образом. С загрузочного стола необработанная труба устанавливается на станину и закрепляется зажимами в каретке 3. Затем начинается вращение резцовой головки и продольная подача заготовки. При выходе обработанного конца трубы из шпиндельной бабки он зажимается в каретке 7 и гидроцилиндром 8 протаскивается через резцовую головку. После этого выключается зажим каретки 7 и обработанная труба скатывается на разгрузочный стол.
Характеристики различных отечественных моделей бесцен-трово-токарных станков приведены в табл. 1, из которой следует, что станки предназначены для обработки труб длиной не менее 3 м. Поэтому их применение для проточки патрубков эффективно только при серийном изготовлении сальниковых и манжетных компенсаторов. При мелкосерийном производстве целесообразно иметь станки с более короткой станиной и широким диапазоном обрабатываемых диаметров труб.
Техническая характеристика бесцентрово-токарных станков |
Характеристика |
Модель |
9330 |
9340 |
9350 |
Размеры обрабатываемых труб мм: |
|
|
|
диаметр |
50-160 |
70-250 |
120-345 |
длина |
3000-10000 |
3100-7500 |
3000-8000 |
Частота вращения шпинделя, об/мин |
16,6-314 |
19-350 |
8-160 |
Мощность электродвигателя, кВт |
75 |
100 |
160 |
Рабочая скорость подачи, мм/мин |
600-4000 |
600-4000 |
600-4000 |
Скорость перемещения каретки, мм/мин |
8000 |
8000 |
8000 |
Габаритные размеры: |
|
|
|
дина |
17,24 |
17,36 |
18,84 |
ширина |
10 |
10,07 |
10,67 |
высота |
1,9 |
2,08 |
2,18 |
Масса, т |
65 |
70 |
80 |
При бесцентровом точении скорость резания 70—80 м/мнн, что в несколько раз превышает скорость резания на обычных универсальных станках. Точность обработки не ниже 0,2% номинального размера, а шероховатость обточенной поверхности не более 2,5 мкм, что удовлетворяет требованиям технических условий на сальниковые и манжетные компенсаторы.
При мелкосерийном производстве патрубки диаметром до 600 мм протачивают на универсальных токарных станках, а более 600 мм — на карусельных. При обработке возможна вибрация заготовки, что ухудшает чистоту поверхности и приводит к поломке резца. На токарных станках заготовку крепят в четырехкулачковом патроне с люнетом и подпирают задней бабкой через специальный конус. На карусельных станках применяют прижимные и распорные приспособления, которые устанавливаются на планшайбах и прижимают или распирают заготовку, тем самым придавая ей дополнительную жесткость при проточке.
Другие детали компенсаторов изготовляют различными способами. Корпус, обоймы для манжет, упорные втулки обтачивают на тех же станках; Т-образные болты изготовляются ковкой или горячен штамповкой с последующей механической обработкой и накаткой резьбы; сальниковая набивка и манжеты поставляются отдельно и устанавливаются при монтаже.